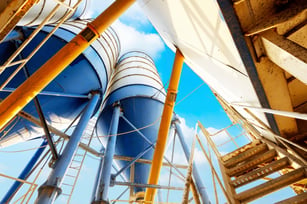
How well a driver spots a truck is more important than any safety solution, and plenty of stories prove this. Still, proper truck spotting is one of the hardest practices to instill in your drivers and operators.
Learn more about the importance of truck spotting and how to promote truck safety at your cement loading facility.
Importance Of Truck Spotting During The Loading Process
Unlike other truck loading processes, the cement loading process requires three steps:
1. Opening the hatch(es)
2. Driving under the dry cement loading spout
3. Closing the hatch(es)
The three-step loading process presents additional opportunities for an accident to occur. Even with the right safety equipment, your operators are still at risk of an injury if a cement truck is mis-spotted.
During the loading process, truck spotting is more important than the safety equipment you have in place. It’s critical that your truck is spotted correctly every single time.
When a cement truck isn’t spotted correctly, the gangway and safety cages won’t align with the top hatches. When drivers attempt to open or close a hatch, they may be tempted to lift away the safety cage. As a result, the driver is exposed to the risk of a fatal fall.
While injuries and death from falls are the most serious ramifications from truck mis-spotting, it’s important to consider other significant consequences. Mining Safety and Health Administration (MSHA) inspectors issue citations, levy fines and have the authority to shut down your facility if your fall prevention equipment doesn’t meet safety standards.
3 Key Ways To Promote Truck Safety
Promoting truck safety in your cement loading facility is challenging. Due to the dangers of cement loading and unloading, it’s important to take extra safety precautions. Here are three of the best ways to boost truck safety at your facility:
1. Use The Appropriate Safety Equipment
Not all safety solutions are created equal, and it’s important to invest in equipment that meets the needs of your cement loading facility.
Before ordering new safety equipment, measure your vehicles and thoroughly understand your loading/unloading processes. This will help your vendor design the correct fall prevention solution for your specifications.
2. Account For Changing Conditions When Spotting
Changing conditions may prevent employees from performing proper truck spotting if instructions are not modified accordingly. Remember to keep your employees up to date on proper spotting techniques while accounting for changes in truck sizes and shapes.
3. Provide Comprehensive Employee Safety Training
Cement loading and unloading is dangerous when your employees don’t know how to properly use the safety equipment. Train your employees on how to safely use all equipment for their jobs as well as proper fall prevention procedures.
Safety equipment alone is not enough to keep your workers safe during cement loading and unloading. By promoting a culture of safety and implementing proper truck spotting procedures, your business will benefit from a safer, more efficient loading/unloading process.
Learn more about the importance of proper truck spotting by downloading this free industry guide from Carbis Solutions.
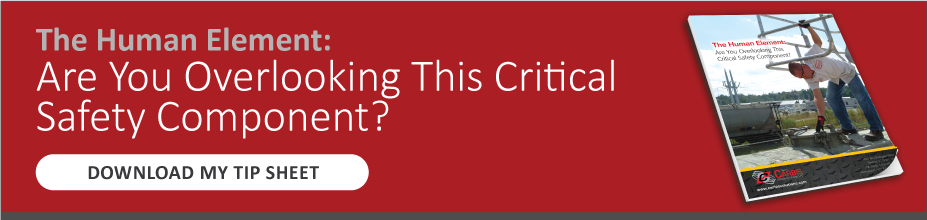