Reducing or eliminating the hazards workers may be exposed to daily is essential to minimizing risk in the workplace. Not only it is the right thing to do, it can have a dramatic impact on the bottom line.
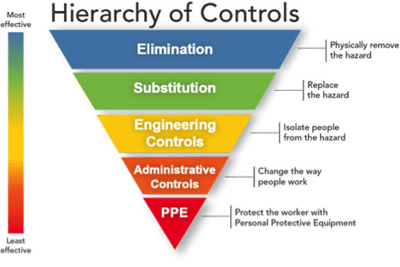
After transportation-related deaths, falls are the number one cause of death on the job, according to the Bureau of Labor Statistics (BLS). Fall-related injury medical costs and workers’ compensation cost U.S. employers approximately $70 billion annually, according to the National Safety Council.
OSHA’s hierarchy of hazard controls illustrates the effectiveness of different approaches to minimize or eliminate hazards in the workplace. OSHA recommends that employers implement injury and illness prevention programs to identify, prevent, and control these hazards. Research demonstrates that “such programs are effective in transforming workplace culture; leading to reductions in injuries, illnesses and fatalities; lowering workers' compensation and other costs; improving morale and communication; enhancing image and reputation; and improving processes, products and services.”1
Workplace risks are present across a broad range of industries and situations from railcar and vehicle spotting to mezzanine access and product movement. Outdated or improperly maintained equipment, a lack of familiarity with safety equipment or procedures, and changing loading or traffic patterns can all cause undue risk in the workplace.
Creating a five-year risk prevention safety plan, that provides safety training on an annual basis, ensures your workplace and employees are up-to-date on the latest safety and fall protection standards, equipment, and practices. A five-year plan provides a blueprint for continued identification, prevention, and control of hazards.
A good equipment safety training program should include:
-
How to perform a basic hazard assessment
-
How to safely operate the equipment at each spot requested
-
How to address a recognized hazard
-
Taking proactive measures to minimize injuries
-
Recognizing mechanical deficiencies through inspection
Changing OSHA requirements also make it challenging for companies to ensure they are OSHA compliant. Workplace changes that render previous training obsolete may make it necessary to retrain employees so that they have the skills and knowledge required to safely access and operate equipment.
Investing in a sound risk prevention plan and safety training provides peace-of-mind, knowing that you are doing the right thing. By proactively identifying and addressing workplace hazards you not only minimize risk but reduce costly workplace injuries.
About Carbis Solutions
Sam Carbis Solutions Group, LLC is the world leader in building customized bulk loading access equipment and structural steel components. Carbis is passionate about partnering with customers to help keep people safer and products flowing. Carbis’ focus on safety began in 1930 when the company invented aluminum fire truck ladders to help keep firefighters safer. Since that time, Carbis has innovated safety and fall protection solutions for a broad range of industries and provided safety training for hundreds of workers to help prevent risk in the workplace.
1. https://www.osha.gov/dsg/InjuryIllnessPreventionProgramsWhitePaper.html