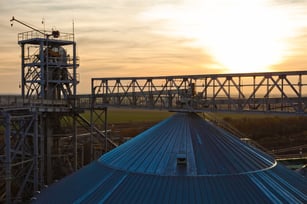
Workplace accidents create a substantial financial burden on your business. Additionally, accidents that result in serious injuries or death may lead to production delays or shut down your facility for a period of time.
Here are five tips to help you improve safety and increase throughput efficiency at your food and beverage facility:
1. Assess Your Site’s Current Fall Prevention Measures
The first step toward increasing workplace safety and throughput is to conduct an honest evaluation of your current fall prevention measures. Ask an outside source to identify the following aspects of your facility:
- Safety equipment that is currently in place
- Shortcomings of your equipment, such as a safety cage that makes it difficult for employees to complete tasks
- Hazardous areas of your safety equipment, such as a gangway without a slip-resistant walking surface
- Old or worn-out equipment that may fail to prevent accidents
2. Install Safety Equipment
Installing safety equipment at your facility goes a long way toward keeping your workers safe without sacrificing throughput efficiency.
Because there’s no one-size-fits-all solution for fall prevention equipment, it’s important to work with a trusted and experienced vendor that can customize a solution to your facility’s specifications.
When looking at safety equipment options, focus on the intuitiveness and accessibility of the solution. Equipment that’s difficult to operate slows down production speed, reducing throughput in the process.
Regardless of whether you need a safety cage or complete safety system, make sure your safety equipment is easy for your employees to understand and operate, so your workers aren’t temped to take safety shortcuts when completing tasks.
3. Keep Safety In Mind When Defining Production Processes
A clear, safety-focused production process helps ensure workplace safety without compromising throughput efficiency. When you have clear processes in place, workers don’t waste valuable time figuring out how to complete each task.
Safety-oriented production processes take potential safety hazards into account. When these risks are accounted for before production begins, the number of slips, trips and falls typically decline, ultimately leading to increased throughput at your facility.
4. Train Employees On Proper Procedures
Although safety equipment and a streamlined production process help reduce the risk of injury and death, it’s simply not enough.
To achieve a safer workplace at your food and beverage facility, it’s critical to educate your employees on the connection between safety practices and throughput. When workers fully understand how a safety culture leads to increased throughput, they take fewer risks, which reduces the likelihood of costly accidents.
5. Conduct Regular Safety Audits
Safety hazards such as liquid on a ladder or a misaligned safety cage greatly increase the risk of slips, trips and falls. Regularly walk through your facility to identify potential hazards and remove these dangers.
When you’re conducting safety audits, review and analyze all of your fall prevention equipment for wear and tear. Worn-out or broken equipment may lead to poor functionality, workplace accidents and unnecessary production delays.
Also, check for process changes or changes in your bulk carriers (trucks, rail cars and isotainers) that might keep your fall prevention equipment from working or fitting properly. These changes often lead to workarounds that aren’t safe for your workers and may hinder throughput.
Keeping your workers safe is critical to increasing throughput efficiency at your food and beverage facility. Fall prevention solutions help improve throughput by reducing workplace interruptions. When fewer accidents happen, your workers are more productive and efficient.
Learn how to keep your workplace moving efficiently while meeting corporate and OSHA standards by downloading this free industry guide from Carbis Solutions.
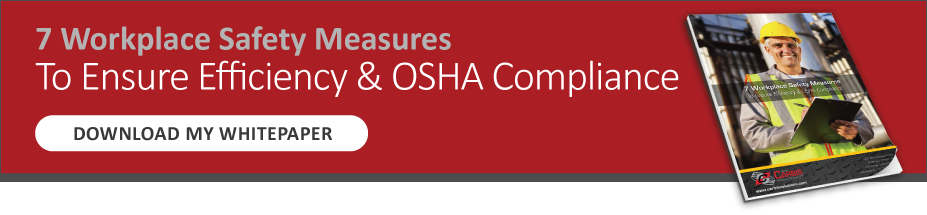